Infrastructure
World Class Facilities
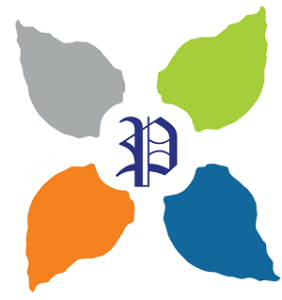
The company believes in bringing the best technology to its optimal use. High efficiencies and skilled manpower contribute to the success of a company and Paramount is a testimony to this virtue. Our investments in human capital, manpower training & the best use of automations have excelled in winning over run of mill competition.
The company’s manufacturing of cotton grey fabrics is done through a versatile and modern state of art Airjet Technology using high speed shuttleless weaving looms from TOYODA Japan. With over 186 looms, the company weaves fabrics from mid to fine count with high degree of precision and care. Automated mechanisms and fully controlled selvedge motions ensure the fabric is perfect when delivered to its customers. The E-Shed systems on the looms enable quick conversion of fabrics to required patterns and offers just in time deliveries, which is the need of the hour.
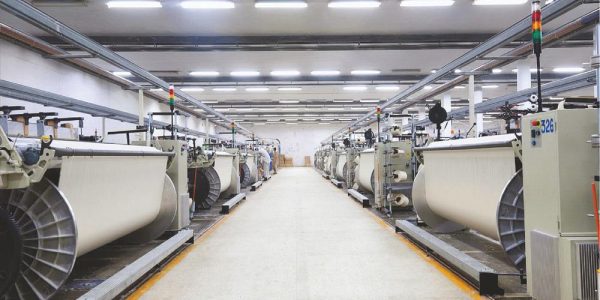
Machineries
144 Toyoda Airjets & 42 Picanol Rapier Machines enable the company to produce designs of exquisite class per demand by world class designers. With over 20 shafts, 20 frames and 8 pre-winders, the looms are best fit to weave high quality yarn dyed fabrics, 100% Linen & Linen Dyed Mélanges and Soft twist performance fabrics with multiple wefts. The versatility of these machines is unparalleled when it comes to the design aesthetics in business. The use of multiple fibers like Soy Bean, Bamboo, Cashmere, Mulberry Silk, Natural Dyed Yarns in cotton & viscose, recycled fibers as well as employment on technical fibers like Kevlar, Glass, Aramid, Para-aramid, Meta-aramid, High Tenacity Polyester, Carbon, Mesh etc. are put to best use.
The company’s preparatory department is fully equipped with the most modern KARL MEYER Sizing Machines with the maximum creel capacity to size ends up to 22500 in one beam and also optimize the performance-production matrix with the modern sow box and automated PLC Controls. The 2 warping machines enable constant feeding to the sizing machine running 24/7. The warp leasing machine from TODO enables the company to lease its ends to prevent any cross ends for high creel capacities. The sizing machine is custom built to size counts from 40/1 NE upwards to 220/2 NE from normal to high and low twist yarns. The fabrics are graded using automatic defect pinning machines in the new state of art warehouse where demerits are controlled to the last degree and 99.99% accuracy level is tagged on the fabric through a sophisticated software that later pins to the in house ERP for easy defect tracking.
Inspection & Warehouse
The warehouse has provisions to roll, bale and pallet its fabrics based on customer needs. Custom packing like Double Folding, Fold Baling, Fixed Piece lengths are available on demand. The factory follows a strict American 4 Point System (ASTM) on grading. The investments into modern machinery like UV Chambers for contamination checking, batch lot sample dyeing to check finished fabric for any defects not visible in grey has resulted in enhanced reputation. The company has a modern doffing warehouse where packed goods are transported to the finished fabric warehouse through overhead trolley and a telescopic conveyor to despatch directly to the containers. Bar code readers & ultrasonic conveyors help store, arrange and re-align rolls and pallets automatically in the warehouse. The company is able to store close to 50 containers (40ft.) of merchandize assorted customer and fabric sort wise to fulfil peak demand and store more for off peak.
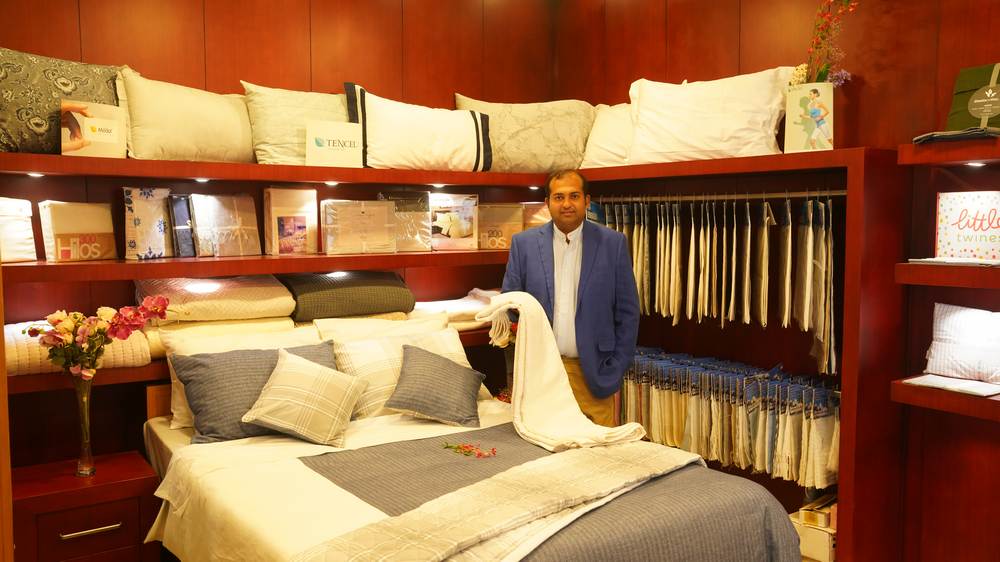
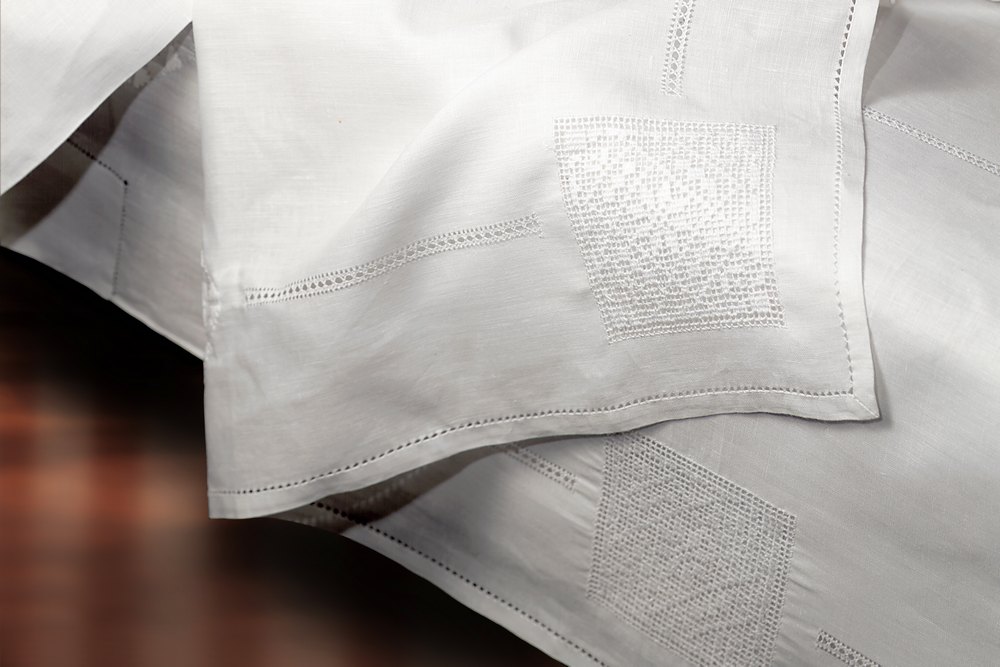
Made-up (Cut & Sew)
The company’s made up division houses over 144 JUKI-Single Needle Machines & 60 JUKI-Double Needle Machines, 18 Z/Zag Machines, 9 Embroidery & 14 Picotting / Baratta Edging machines besides the multifunctional hem attachment machines. The state of art INA Hangers transport material without any hand contacts ensuring highest hygiene and safety of products. Creases, hand folds, stains & bow/skew issues are completely avoided and taken care during its sophisticated production & checking lines.
Quilting Department
The company produces about 4000 sheet sets a day in the most complex and difficult hem guides. The Quilting department quilts about 120 quilts a day with cotton, linen, organic, fair trade bases and wading sourced most ethically and sustainably from GOTS/FLO Sources.
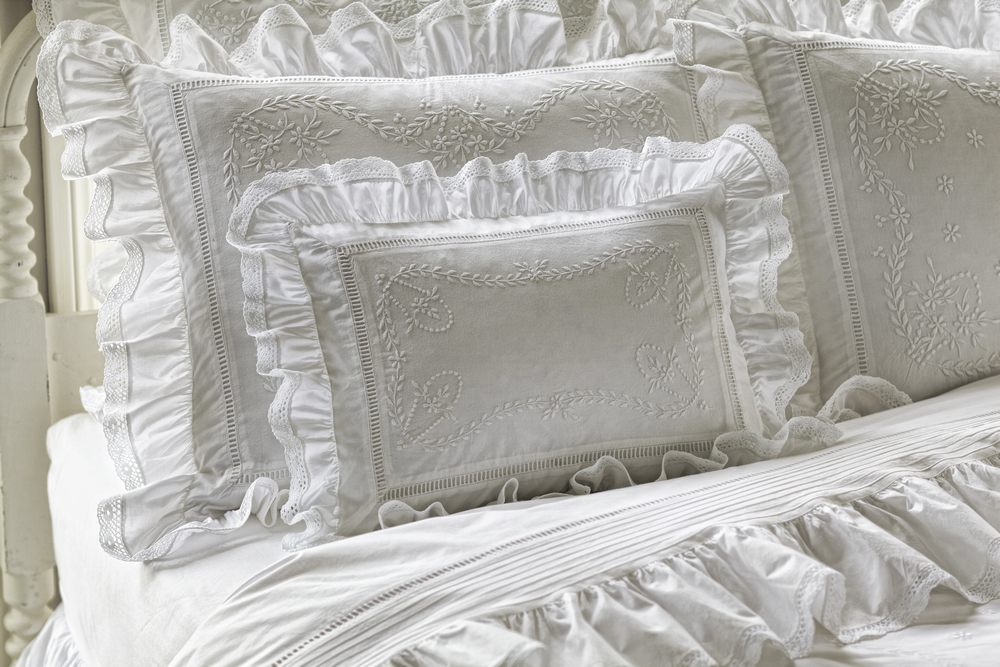
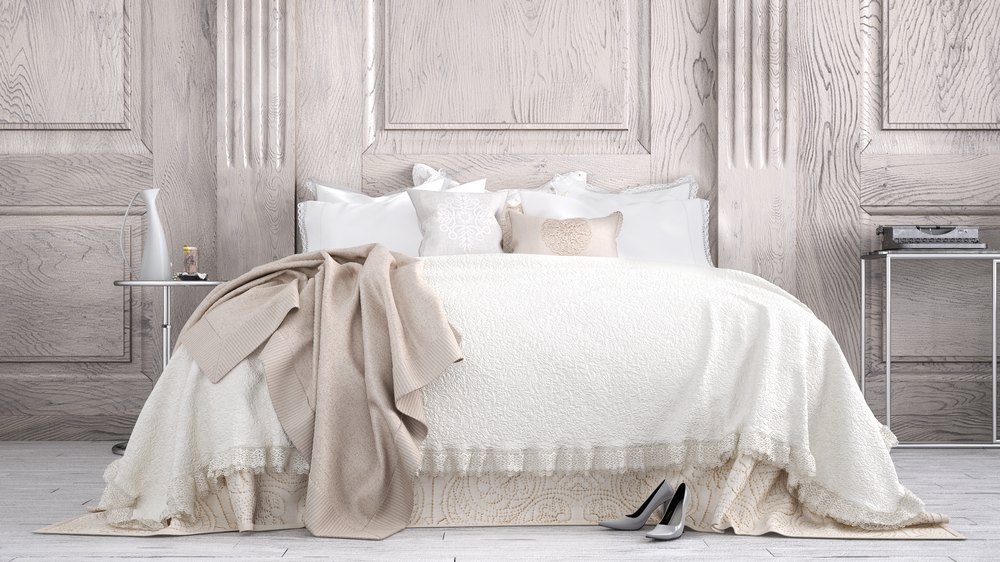
Quality Control
The Checking and Trimming departments have the most sophisticated pneumatic air suckers and thread trimmers to make work easy and efficient reducing human error.
Packing
The packing departments are automated including bar coding and reading with box or pallet packing options. The metal detector machines are put to best use in the packing department with every single piece going through a needle detector process ensuring highest health and safety measures in the system.
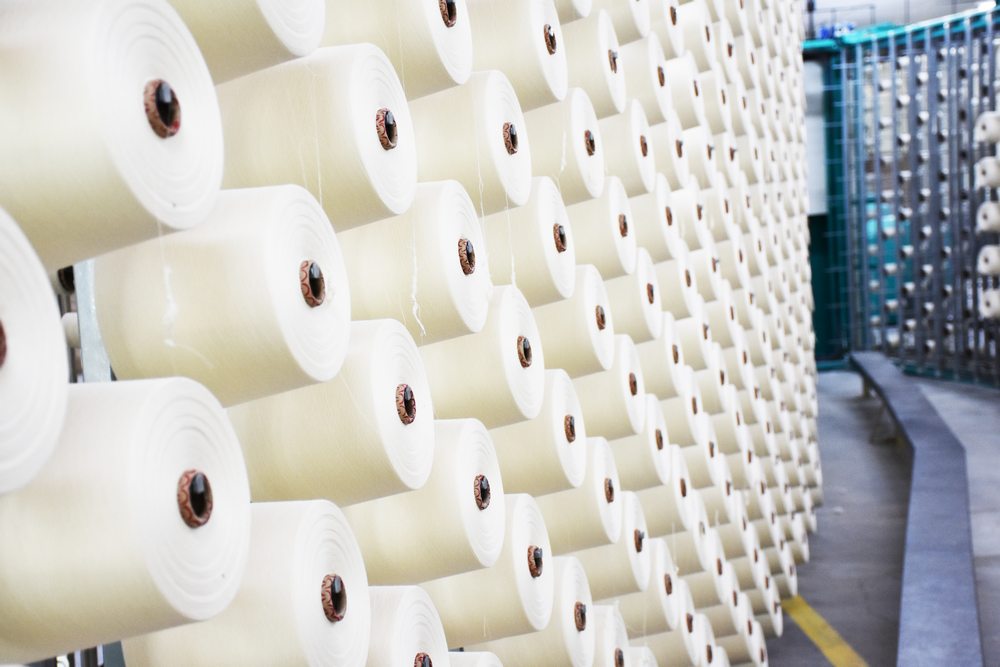
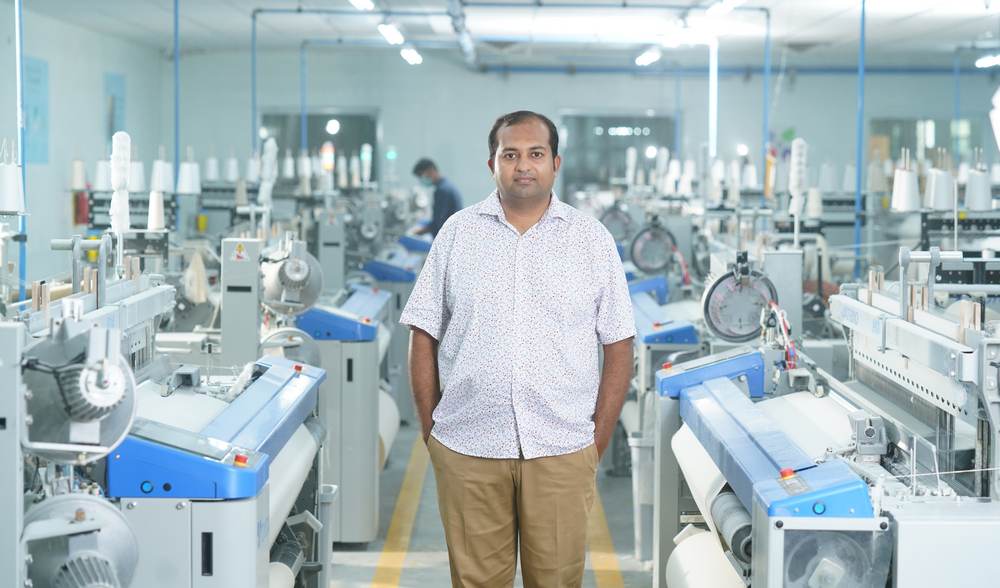
Training
A training department constantly trains women workforce from nearby villages to gain livelihood and also gives opportunities for part time work to make their living. A comprehensive training lab along with real time instruments and machineries where labors are trained hands on real environment.
Ambience
The entire powering of the factory is done through a hybrid SOLAR PLANT of 2.2 MW just next to the facility. The company in addition treats all of its water inside to use for the lush green plantation around it. The importance of high quality working environment, fresh air and rich soil has never been pronounced more than this and our endeavor to deliver a green product doesn’t just start with seed cotton, but goes much beyond. A ZLED water recycling facility, Multiple R.O Plants to reduce waste water, Sewage treatment plants, OZONE-ION plant for purification of waster recycled water, centralized rain water harvesting system to connect every pipeline to the major reservoire, BIO-Gas plant to fuel needs of the canteen including organic farming that helps utilize milk, vegetables & fruits for the company’s labor and staff canteens.
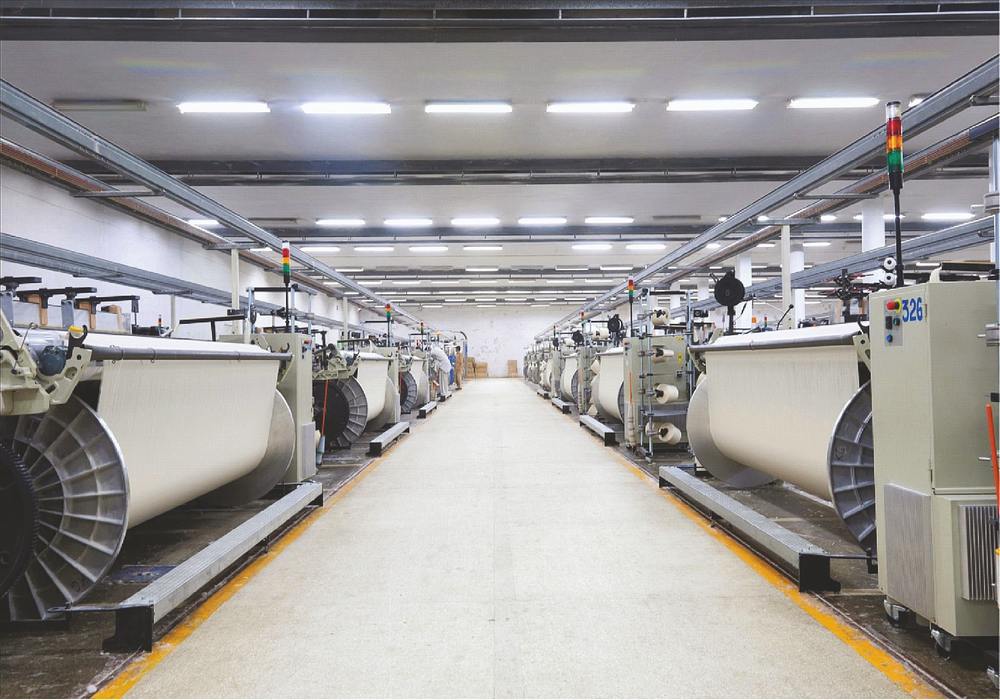